“PAXTAKOR TEKS” LLC
-
Product category: Textile
-
Region:Tashkent
Company profile
Indicators |
Information |
Name |
«Paxtakor teks» LLC |
Business type |
Manufacturer/Exporter |
Main products |
Textile products |
Year established |
2017 |
Total employees |
1000+ |
Country/ region |
Tashkent, Uzbekistan |
Ownership |
Private |
Occupied area, ha |
11200 |
Certifications |
ESG standards |
Main markets |
Japan Turkey Switzerland India |
“PAXTAKOR TEKS” LLC
Joint Venture “PAXTAKOR TEKS” LLC is a modern, dynamic enterprise that is specialized in the production of ring spinning carded yarn using as raw materials the best cotton varieties grown in Uzbekistan.
Production
Innovative technology used to loosen bales, guarantees efficiency in the scutching compartment. When choosing equipment, the focus is mainly focused on a reliable, convenient-to-maintain machine, designed for maximum performance.
In addition to raw materials and the possibility of a spinning machine, the quality of spinning is primarily influenced by the work of specialists. The company PAXTAKOR TEKS employs experienced and qualified employees who know their work perfectly and have the appropriate international qualifications. All this together allows us to achieve and maintain a high level of yarn quality at maximum productivity.
To obtain high-quality products at the final stage, an automatic winding machine called “MURATA Process Coner II QPRO Plus” is used, which ensures high quality and productivity. This model with improved and various convenient options allows you to fully satisfy the need of the customers. A specialized machine ensures the stability of the process of winding the yarn from the beginning to the end using a special PC module. To maintain quality, the machine uses a quality control system – Uster Quantum3
Laboratory
The laboratories of our production use the equipment “Uster Technologies” – the world leader in the field of textile testing and quality control.
The proven technology of «USTER® JOSSI VISION SHIELD 2» and «USTER® QUANTUM 3» eliminates extraneous substances at the end of two yarn processes. «Uster Technologies» is the only provider of this integrated solution. Reliability «USTER® JOSSI VISION SHIELD 2» is a decisive factor, supported by high-quality design and reliable software that guarantees high efficiency over its entire life cycle.
The newest solution, “Uster Tester 6,” covers absolutely all the processes of the spinning mill and is an important step forward for managing high-quality production of the spinning mill. “Uster Tester 6” includes “Uster Quality Expert” – the most important tool for quality management and with the possibility of creating a completely new “Total Testing Center”. Accurate lab test results using Uster Tester 6 are the starting point for complete testing. This data is combined with real-time information from yarn cleaners that control 100% mill production.
Modern technological processes allow the company “PAXTAKOR TEKS” LLC to complete large volumes of orders in the shortest possible time and at the same time, maintain the quality of all types of products. The production capacity of the enterprise is 9,000 tons of yarn per year. The company is equipped with the most advanced equipment of such well-known manufacturers as “Rieter”, “Sieger Spintech Equipment”, “Murata Machinery”, “Temsan Air Engineering” and a quality control system called “Uster Technologies”.
Manufacturing process
There are three main spinning processes: cotton, worsted or long staple, or wool. Synthetic staple fibers can be obtained using any of these processes. Since more yarn is produced in the cotton process than in the other two, its production is described below.
Fiber preparation
The fibers are delivered in bales, which are opened manually or by machine. Natural fibers may require purification, whereas synthetic fibers only require separation. The collector weakens and separates the fiber lumps, and also cleans the fiber if necessary. In some cases, it may be necessary to mix different staple fibers. Blending can be done during the formation of a circle, during cardation or extrusion. The amount of each fiber is carefully measured, the level of quality is constantly maintained.
Carding
The carding machine is equipped with hundreds of thin wires that separate the fibers and pull. A thin fiber web is formed, which, moving along it, passes through a funnel-shaped device, forming a thread in the form of a rope of parallel fibers. Mixing can occur by connecting circles of different fibers.
Combing
When smoother and thinner yarns are required, the fibers are subjected in parallel to an additional method. The comb device places the fibers in parallel form with short fibers falling out of the strand.
Pull process
After scratching, the pulp is called a ribbon, combining several threads before the process. A series of rollers rotating at different speeds draws the tape into one more uniform strand, which bends slightly and is fed into large cans. Card tapes are obtained after carding.
Next, the tape is fed and passes through a machine called a roving frame, where the fiber yarns are additionally lengthened and receive additional twisting. These strands are called roving.
Spinning process
Predominant yarn forming systems are ring spinning and open-end spinning. During the ring rotation, roving is fed from the reel through the rollers. These rollers lengthen the roving, which moves down.
The tape is fed through a machine called a roving frame, where the filaments of the fibers are additionally lengthened and receive additional twisting. Predominant yarn forming systems are ring spinning and open-end spinning. Open rotation skips the roving step.
Open rotation skips the roving step. Instead, a strip of fibers is fed into the spinner by air flow. The tape is fed into a rotating nimbus, which separates the fibers into a thin stream and is transferred to the rotor by a stream of air through a pipe or channel and is deposited in a V-shaped groove along the sides of the rotor. A constant stream of new fibers enters the rotor, is distributed in the groove and is obtained in the form of a formed yarn.
Quality control
Automation makes it easy to get high quality thanks to electronics, which controls operations, temperature, speed, turns and all the necessary technical processes in general.
Product catalog of this supplier
Categories:
“PAXTAKOR TEKS” LLC
Address: Tashkent, Yashnabad district, st. Dzharkurgan, 76
Contacts: +998 71 283 98 97
Email: [email protected]
Website: www.paxtakor-teks.uz
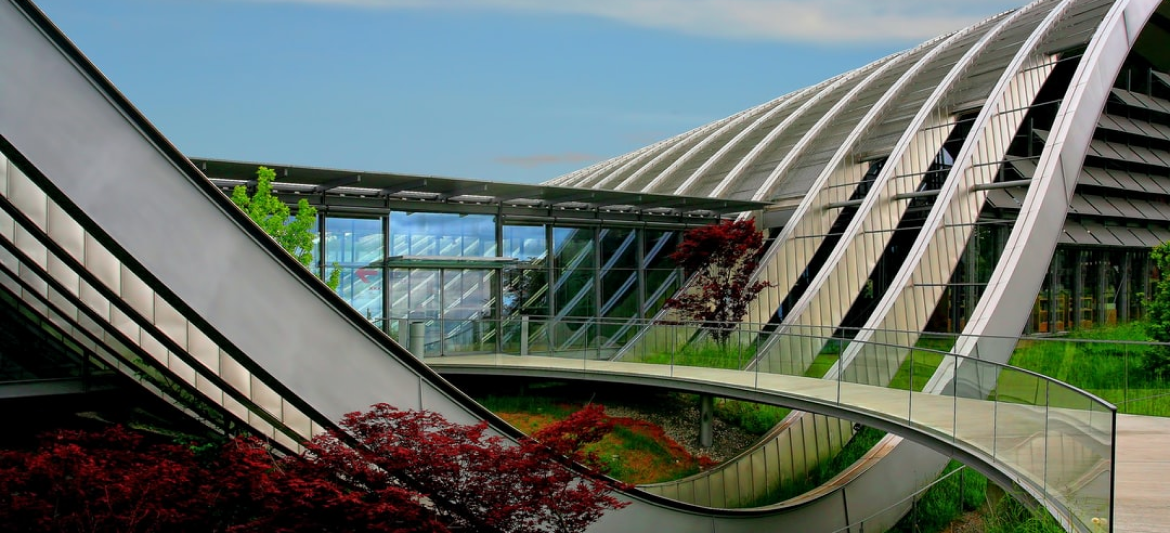